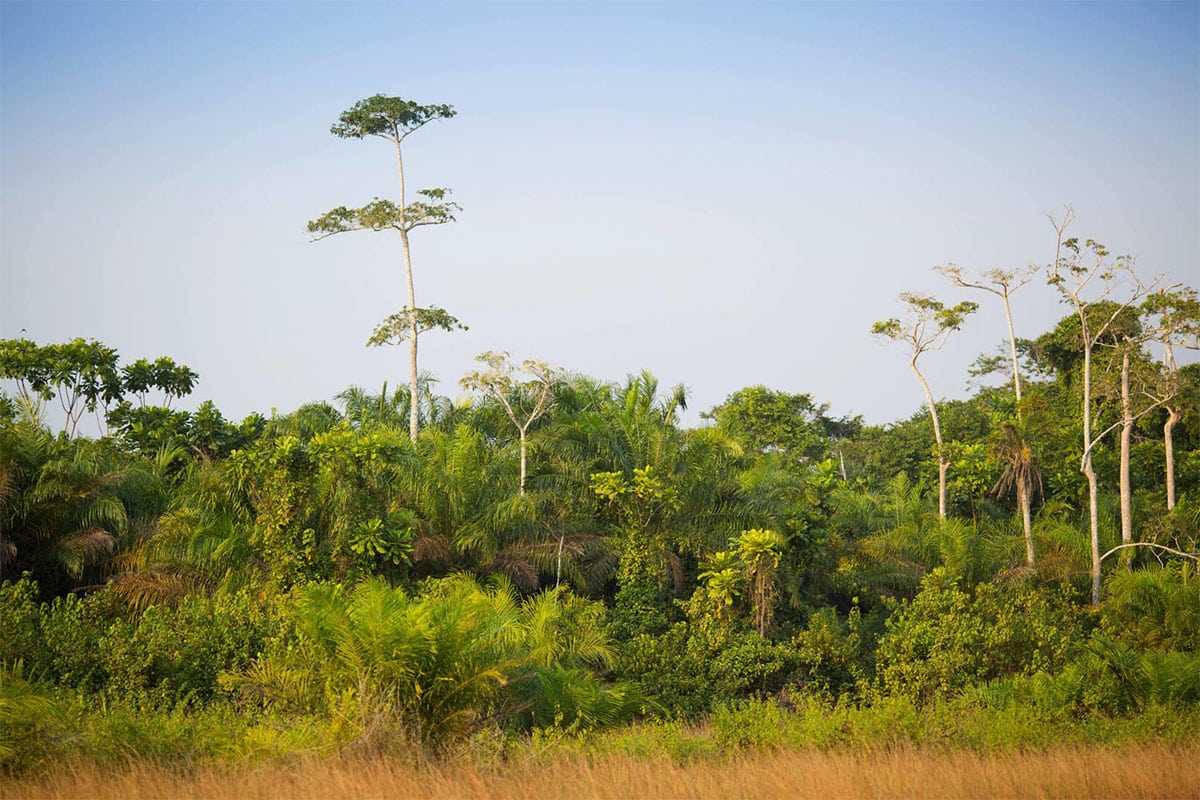
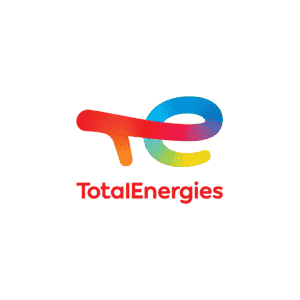
BaCaSi project : carbon sinks in Congo
A large-scale afforestation operation has been kicked off by TotalEnergies on the Batéké Plateau in partnership with the Republic …
The objective is to provide Polyethylene (PE) users with a “drop-in” solution that is a perfect substitute (in terms of mechanical performance, food safety approval, etc.) for conventional fossil fuel-based PE while reducing considerably its environmental footprint (LCA). PE carbon footprint reduction will come from substitution of fossil oil by a less carbon intensive feedstock.
TotalEnergies’ Polymers activity has fully committed to taking on this challenge by innovating to reduce the carbon footprint of its products, particularly polyethylene (PE), by using feedstocks other than fossil oil. With this in mind, TotalEnergies worked with L’Oréal and Lanzatech, both players in the value chain, to develop this ambitious project. The first major deliverable of this world premiere involved a pilot-scale proof of concept of the very first sustainable packaging produced from captured and recycled carbon emissions.
The ultimate objective of this project is the industrial production of PE from ethanol, obtained via a biotech process based on the bacterial fermentation industrial waste gas. To achieve this, TotalEnergies is using an innovative dehydration process developed with IFP-EN and Axens to transform ethanol into ethylene, which is then polymerized to turn it into a PE that has all the technical specificities of its fossil fuel-based counterpart.
The aim of the project is to implement a value chain, from the ethanol obtained from recycled carbon produced by a variety of sources (including waste gas from the industry) to the marketing of PE made from this feedstock.
It will enable us to propose plastics that are just as effective and more sustainable than fossil fuel-based solutions, and that fit into a circular economy, including the recycling of the product obtained.
The realization of the pilot-scale proof of concept was a key element, to demonstrate the technological feasibility of the dehydration process needed to transform the ethanol into polymer-quality ethylene.
This innovation paves the way for carbon capture and recycling to produce materials (PE) thereby avoiding industrial waste gas and the use of fossil resources. In addition, this PE is perfectly recyclable at the end of its lifecycle via existing and well-established schemes, meaning that it fits into a complete circular value chain.
on which the project has a significant impact
Scopes 1 and 2 – Standard ethylene production
process is replaced by a
process based on the
dehydration of recycled carbon
based ethanol.
The Fossil fuel-based ethylene
coming from a naphtha cracker
is replaced by the ethylene
produced in a dehydration unit
using recycled carbon based
ethanol as a feedstock. The
polyethylene production stage
remains the same whatever the
source of the ethylene.
Scopes 3 et Emissions avoided – The polyethylene made from
recycled carbon-based ethanol
has a lower carbon footprint
(cradle to gate) than the fossil
fuel-based equivalent it is
replacing.
/
> €100 M (amount estimated based on the conceptual study)
2018
Belgique
This project could offer an economic and circular outlet to ethanol produced by biotechnology with a twofold benefit: it helps reduce the carbon emissions of certain industrial activities (CCU approach) and it enables the polymer industry to no longer use fossil oil as a raw material to produce polymer. Owing to these prospects, a number of industries could initiate projects to produce ethanol from waste gas and TotalEnergies could use this ethanol as a substitute for conventional feedstocks obtained from fossil oil refining.
The project and its climate impact potential are reproducible provided that:
Three partners are involved in this project:
The three partners wish to continue working together to produce sustainable plastic on a larger scale and they welcome anyone else ready to commit to using these new sustainable plastics.
david.vandewiele@totalenergies.com
A large-scale afforestation operation has been kicked off by TotalEnergies on the Batéké Plateau in partnership with the Republic …
The Masshylia project aims to produce green hydrogen from solar photovoltaic energy to initially supply the TotalEnergies biorefinery in La Mède. This is the first large-scale…
TotalEnergies is launching a project to transform its Grandpuits refinery into a biorefinery, by installing a production…
In collaboration with Equinor and Shell, TotalEnergies is developing a project in Norway to transport and store CO2 in underground geological formations located off the Norwegian coast.
Al Kharsaah is the first utility-scale solar power plant in Qatar and will help reduce Qatar’s CO2 emissions while meeting its increasing electricity demand …
The project consists in building three gigafactories for the production of battery cells and modules for electric vehicles (EV).
The Seagreen Offshore Wind Farm project aims at generating green electricity from wind energy. Seagreen will be Scotland’s largest …
AFEP (Association of French large companies) is an association representing 111 of the largest companies operating in France. It participates in the public debate with the ambition to provide pragmatic answers in favour of the development of a competitive and sustainable French and European economy, conducive to the growth of all companies.