Installation of a boiler unit at Kamenski Sugar plant
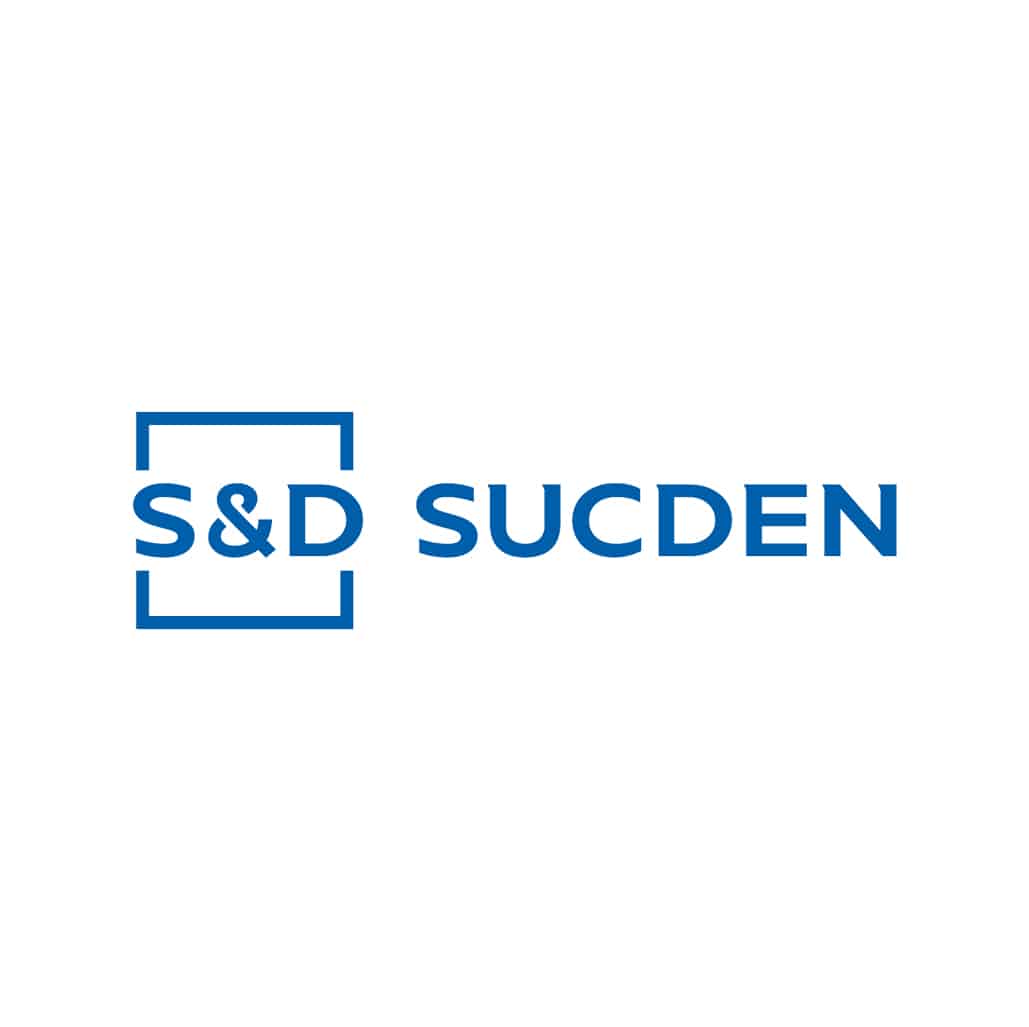
Sucden optimizes industrial processes – installation of a boiler unit – in a sugar plant in Russia to reduce gas consumption and environmental footprint.
Main project's drivers for reducing the greenhouse gas (GHG) emissions
Energy and resource efficiency
Energy Decarbonisation
Energy efficiency improvements
Improving efficiency in non-energy resources
Emission removal
Financing low-carbon issuers or disinvestment from carbon assets
Reduction of other greenhouse gases emission
Project objectives
This project aims at reducing GHG emissions of the sugar plant by reducing gas consumed in the industrial process.
The success of this project requires the installation of a new boiler unit. It will imply a change in the input of products at the key stage of crystallization.
Evaporation in sugar plants has two main functions:
- It provides low pressured steam in different parts of the sugar plants depending on thermal level (pressure/temperature) from 130° to 90°C. This steam results from the electricity in turbo generator.
- It condenses the sugar beet juice from 17.5% up to 68-72% of dry matter (syrup). Mass of the syrup resulting from evaporation is then only about 25% of the incoming juice, which is done in 5 steps or evaporation phases.
General principle:
The juice is heated until boiling. Water steam produced is reintegrated to feed other equipment in the factory, and juice is getting more condensed (syrup).
In a single evaporator system, the steam produced by the juice boiling is not reused. For each kg of evaporated water, there must be provided 1 kg of steam heating. This process generates GHG emissions that could be avoided, and this is the reason why we looked for improvements.
Multiple evaporator system enables a bigger evaporation of water with the same amount of initial steam. In this system, 1 kg of steam input in the 1st stage evaporates 1 kg of juice. This same kg of water also evaporates 1 kg of water in the next stage and so on.
To allow reduction of steam consumption in a sugar plant through a multiple evaporator system, the global output of evaporated water must remain below each level to keep positive savings of energy and GHG emissions.
Specific case of Kamenski plant:
- At Kamenski sugar plant, evaporation at the 4th stage was poor after the recent increase of the plant production capacity. This resulted in an accrued consumption of energy and GHG emission for the 3rd evaporation stage.
The boiler unit added in Kamenski aims at increasing the evaporation capacity of the 4th stage to get a warmer steam and thus reduce the use of steam produced from gas consumption.
Emission scope(s)
on which the project has a significant impact
- Emission scopes
- Description and quantification of associated GHG emissions
- Précisions sur le calcul
Scope 1
Émissions directes générées par l’activité de l’entreprise.
Scope 2
Émissions indirectes associées à la consommation d’électricité et de chaleur de l’entreprise.
Scope 3
Émissions induites (en amont ou en aval) par les activités, produits et/ou services de l’entreprise sur sa chaine de valeur.
Absorption d’émissions
Création de puits de carbone, (BECCS, CCU/S, …)
Émissions évitées
par les activités, produits et/ou services de l’entreprise ou par le financement de projet de réduction d’émissions.
Scope 1 – The project will cut gas consumption by 1m3 for each ton of sugar beet processed.
- Quantification: -1.9ktCO2eq/an
This investment will reduce GHG emission by reducing the gas consumption by 1m3 per ton of sugar beet processed.
In 2020, the plant produced 102,918t of CO2 for 955,756 tons of beet processed.
Given that 1m3 of gas represents 1.9885 kg of CO2 emissions (1m3/year x 0.0097 MWh PCI/m3 * 205kg CO2/MWh PCI = 1.9885 kq CO2 eq).
In 2021, a comparable volume of beet processed would avoid 1,900 tons CO2, i.e a reduction of 1.8%.
1 m3/tb*900,000 tb*5.65 rubles/m3 = 5,000,000 RUB/year of savings
Les points clés
Montant de l’investissement réalisé
400 000 €
Date de démarrage du projet
2020
Localisation
Russia
Niveau de maturité
Test prototype en laboratoire (TRL 7)
Test en réel (TRL 7-8)
Prototype pré-commercial (TRL 9)
Mise en œuvre à petite échelle
Mise en œuvre à moyenne ou grande échelle
Rentabilité économique du projet
Court terme (0-3ans)
Moyen terme (4-10 ans)
Long terme (> 10 ans)
Images / Vidéos
The project will contribute to ODD 9 – Build resilient infrastructure, promote sustainable industrialization and foster innovation : the industrial process will be optimized to reduce environmental footprint.
This type of projects can be realized in all the plants of the Group.
Contacter l'entreprise :
sustainability@sucden.com
Sucden’s other projects :
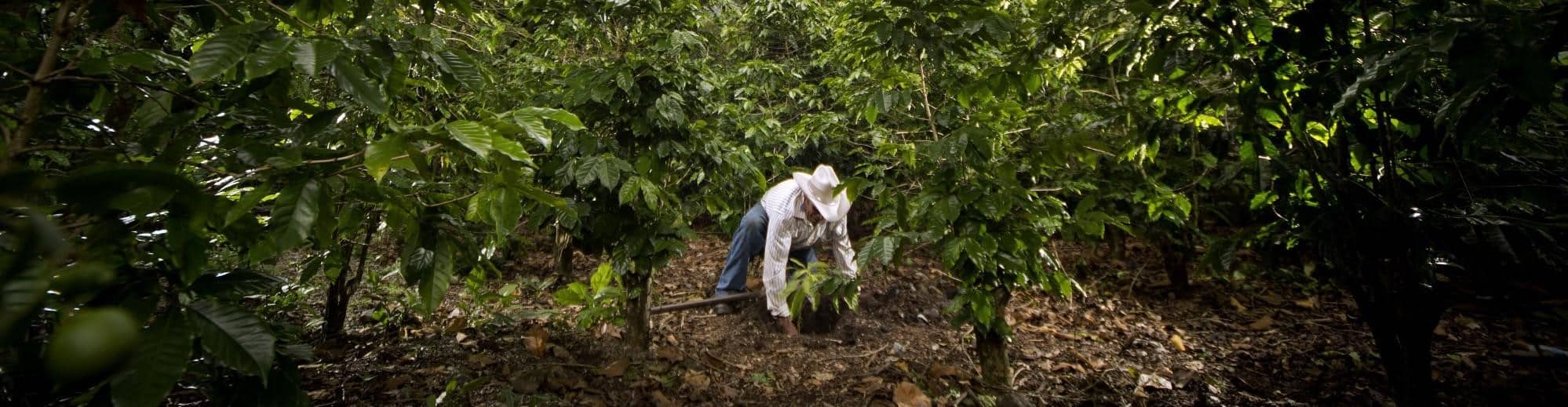
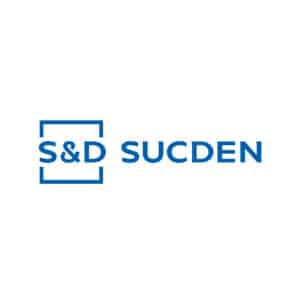
PUR Project : an Agroforestry Project
Sucden is developing a community-based agroforestry project in Côte d’Ivoire with a cooperative of cocoa farmers. The goal of the project is to plant 40,000 trees over two years with 400 farmers. The main objective of the project…