Increase the steel recycling
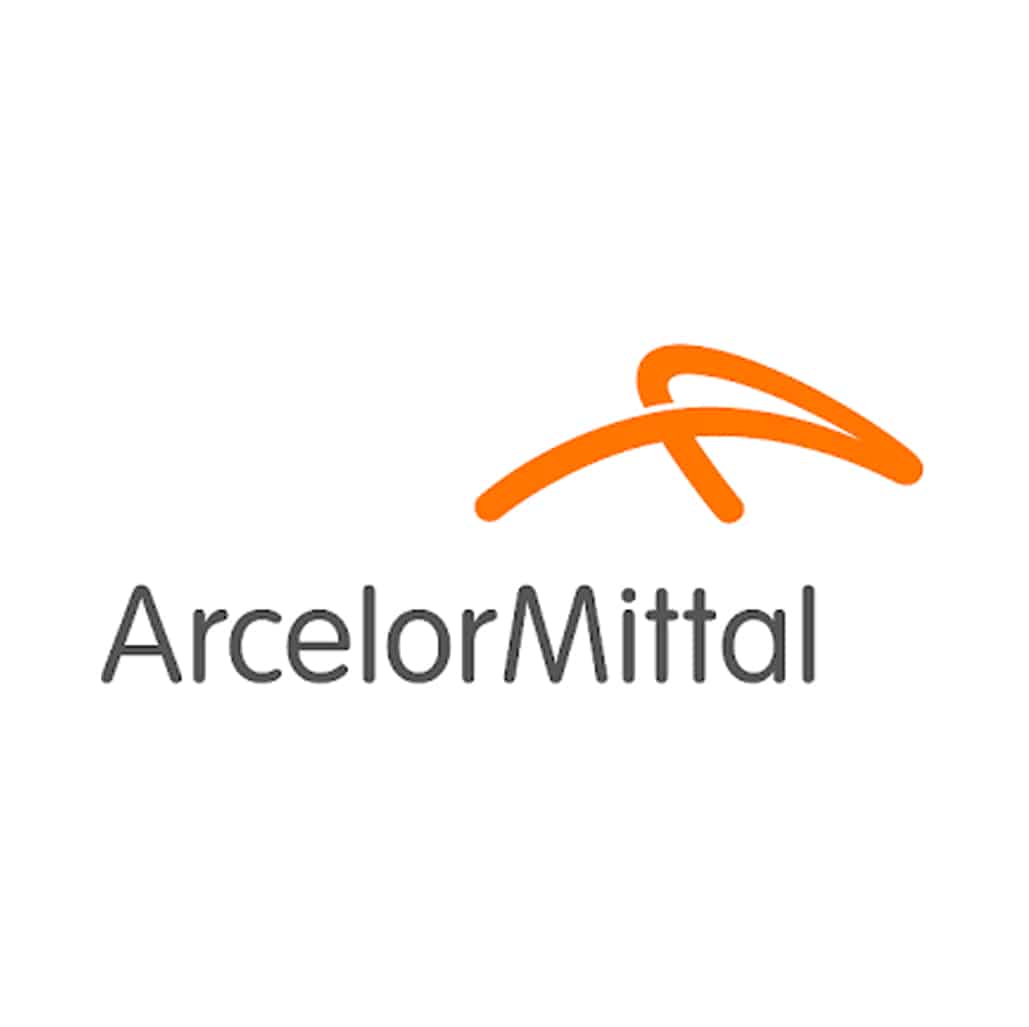
ArcelorMittal's project aims to increase the part of used steel (scrap) in the production process of the Fos-sur Mer steel mill. This involves adapting the scrap processing capabilities as well as installing an electric furnace (ladle furnace) downstream of the converter to compensate for the cooling of the liquid steel associated with this addition.
Main project's drivers for reducing the greenhouse gas (GHG) emissions
Energy and resource efficiency
Energy Decarbonisation
Energy efficiency improvements
Improving efficiency in non-energy resources
Emission removal
Financing low-carbon issuers or disinvestment from carbon assets
Reduction of other greenhouse gases emission
Project objectives
The aim is to increase the part of recycled steel (scrap) in the steel production process in order to: • Reduce blast furnace melt production and associated CO₂ emissions; • Promote the recycling of used steel - pre and post-consumption steel now exported in large quantities.
The steel produced in the Fos-sur-Mer plant is produced in blast furnaces from iron ore and coal (in the form of coke and injection). The cast is then processed in a converter. In order to limit the consumption of iron ore and coke, whose use results significant CO₂ emissions, it is possible to incorporate used steel – or scrap – into the production process. The larger the scrap, the smaller the quantities of raw materials needed.
Currently, the Fos-sur-Mer site produces nearly 4 million tonnes of steel. Nearly 500,000 tonnes of scrap are now uses, including 400,000 tonnes from internal recycling at the plant and 100,000 tonnes purchased outside. The aim is to increase the part of scrap purchased outside to 400,000 tonnes per year (or 8,000 tonnes of scrap metal in total to produce the 4 Mt of steel). To achieve this, several steps are needed:
- Steel Recycling – Scrap Management
The increase in the share of scrap in the production process requires a total resizing of the means of receiving, processing, processing and injecting the scrap into our converters.
These new needs will be supplied by so-called “noble” scrap but also by low-quality scrap containing a greater proportion of residual elements (aluminum, copper, non-ferrous: wood, plastics, etc.). It is therefore necessary to review the site’s capacity to prepare / clean the scrap before charging.
This involves, in particular, the resizing of the means for feeding the scrap into the converters (the “augets”) and the setting up of means aimed at densifying the scrap (sorting, compacting, etc.).
- Steel Recycling – Installing an electric oven (ladle furnace)
The transformation of cast iron into liquid steel is carried out in an oxygen converter. The first step is to charge liquid cast iron and the steel coming from recycling (cold). The converter will decarburize (oxygen blast) the cast iron and increase the temperature of the mixture and thus melt the scrap.
The temperature target depends on the production cycle up to continuous casting. Integrating an electric heating means, such as the “ladle furnace”, between converter and continuous casting increases the proportion of scrap iron loaded by targeting lower temperatures at the end of blowing.
Emission scope(s)
on which the project has a significant impact
- Emission scopes
- Description and quantification of associated GHG emissions
- Clarification on the calculation
Scope 1
Direct emissions generated by the company's activity.
Scope 2
Indirect emissions associated with the company's electricity and heat consumption.
Scope 3
Emissions induced (upstream or downstream) by the company's activities, products and/or services in its value chain.
Emission Removal
Carbon sinks creation, (BECCS, CCU/S, …)
Avoided Emissions
Emissions avoided by the activities, products and/or services in charge of the project, or by the financing of emission reduction projects.
Scope 1 – Use of recycled steel in the manufacturing process
- Quantification : – 680 ktCO2/year
Scope 3 – Consumption of local scrap metal as a substitute for imported coals and ores
- Quantification : – 25 ktCO2/year
Each tonne of recycled steel reduces the use of melt from blast furnaces by about 0.9t (production generates about 1.9 t of CO₂eq per tonne of cast iron). The additional electricity consumption (43,000 MWh/year) results in emissions of around 2,461t of CO₂eq/year taking into account the average FE of electricity in France (57.1 kg CO₂/MWh).
The site’s CO₂ emissions are # 7,659 kt CO₂ in 2019.
Gains if the investment is decided in early 2021
- 680 kt CO₂/year in 2023, so about 10% of the site’s emissions
Key points
Invested amount
85 M€ (including 63 M€ invested by ArcelorMittal)
Starting date of the project
2020
Project localisation
Fos-sur-Mer, Bouches du Rhône.
Project maturity level
Prototype laboratory test (TRL 7)
Real life testing (TRL 7-8)
Pre-commercial prototype (TRL 9)
Small-scale implementation
Medium to large scale implementation
Economic profitability of the project (ROI)
Short term (0-3 years)
Middle term (4-10 years)
Long term (> 10 years)
Illustrations of the project
This project allows to:
- Develop local steel recycling channels
- Decrease scrap exports
- Reduce imports of coal and minerals
- Reduce water and air emissions associated to the cast iron industry (coke plant, agglomeration, blast furnaces)
The potential is specific for every steelwork.
A second step is being considered to further increase the share of recycled steel through a second partial electrification of the process.
Partnerships are being developed and are mainly aimed at securing the supply of scrap metal to the site.
For example, a ship dismantling line is being developed with Topp Decide in the Grand Port Maritime de Marseille, to produce good quality scrap metal.
Contact the company carrying the project :
damien.chambolle@arcelormittal.com bruno.lesaulnier@arcelormittal.com