Digital energy at the heart of the Factory of the Future
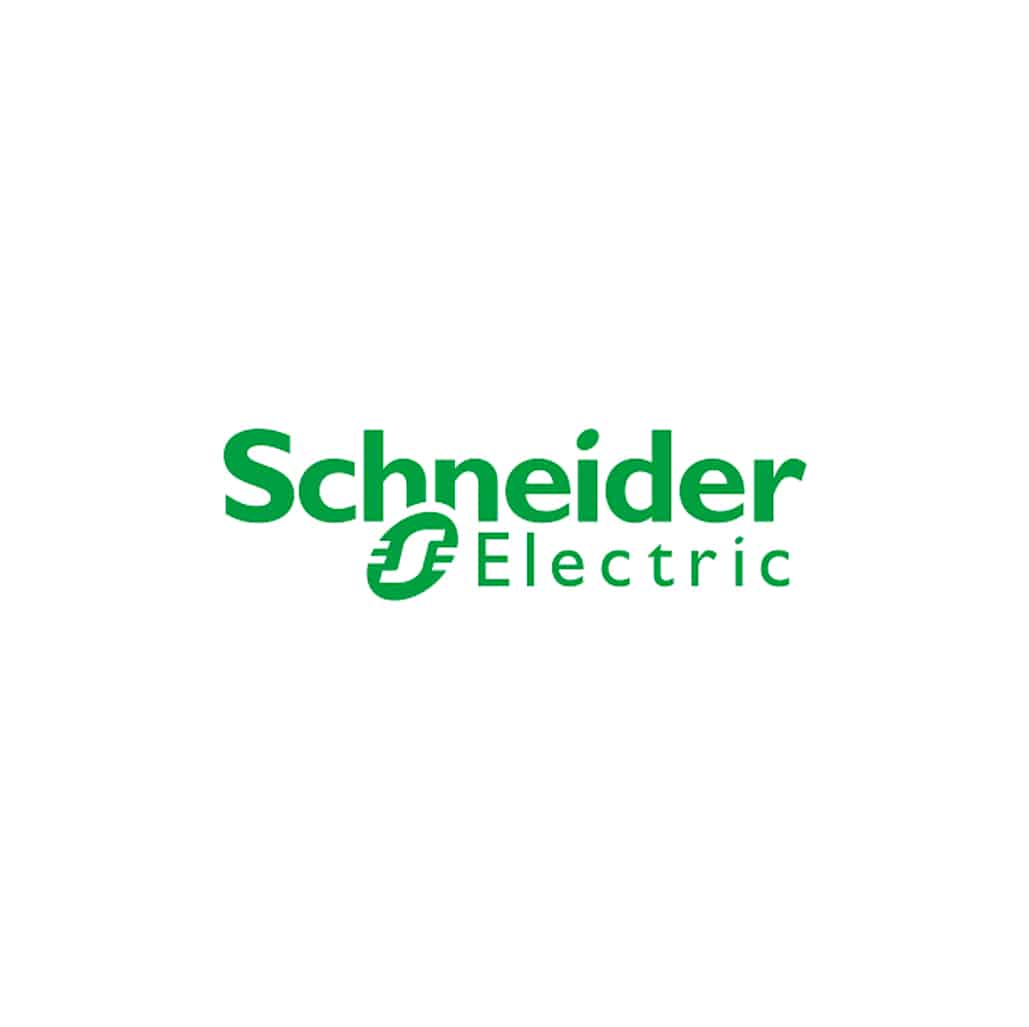
As part of its "Factory of the Future 4.0" program, Schneider Electric deploys energy monitoring systems on its industrial and logistics sites that optimize energy consumption and reduce associated CO2 emissions.
Main project's drivers for reducing the greenhouse gas (GHG) emissions
Energy and resource efficiency
Energy Decarbonisation
Energy efficiency improvements
Improving efficiency in non-energy resources
Emission removal
Financing low-carbon issuers or disinvestment from carbon assets
Reduction of other greenhouse gases emission
Project objectives
Reduce energy consumption by implementing digital solutions that optimize the operation of industrial processes and building use.
Schneider Electric innovates to invent the Factory of the Future 4.0. The Fourth Industrial Revolution is a tremendous lever to accelerate the transformation of industry towards green and sustainable operations.
Energy management is at the heart of this industrial revolution: Thanks to the digitization of its energy, the company optimizes its consumption and decouples its industrial production from the generation of greenhouse gases. Since 2018, Schneider Electric has deployed its EcoStruxure digital platfo rm to reduce energy consumption.
For example, in its smart factories and smart distribution centers, the company has reduced its energy costs from 5% to 30% and its maintenance costs from 30% to 50%. The use of EcoStruxure solutions have also reduced production interruptions and quality problems by about 15%.
In concrete terms, Schneider Electric has deployed energy monitoring systems for natural gas (25% of consumption) and electricity (70% of consumption) on its industrial and logistic sites.
Thanks to networked meters linked to the company’s EcoStruxure digital architecture, Schneider Electric is able to optimize its energy consumption and CO2 emissions. Supervision systems provide energy dashboards, both global and use-specific, as well as automatic alerts in the event of drift. This allows for robust and responsive monitoring, enabling easier decision-making and faster corrective action. The integration of monitoring into the management processes of the plant enables energy to be put at the heart of industrial performance and can offer new business opportunities for factories by increasing their profitability and productivity.
Emission scope(s)
on which the project has a significant impact
- Emission scopes
- Description and quantification of associated GHG emissions
- Clarification on the calculation
Scope 1
Direct emissions generated by the company's activity.
Scope 2
Indirect emissions associated with the company's electricity and heat consumption.
Scope 3
Emissions induced (upstream or downstream) by the company's activities, products and/or services in its value chain.
Emission Removal
Carbon sinks creation, (BECCS, CCU/S, …)
Avoided Emissions
Emissions avoided by the activities, products and/or services in charge of the project, or by the financing of emission reduction projects.
Scope 1 – Digital monitoring and optimization of energy consumption
- Quantification : 7 000 tCO2
Scope 2 – Digital monitoring and optimization of energy consumption
- Quantification: 40 000 tCO2
In 2020, Schneider Electric’s energy efficiency program achieved 10.6% energy efficiency compared to the 2017 reference year, i.e. 3.5% efficiency on average per year on all sites.
From 2017 to 2019, emissions (scopes 1 and 2) from Schneider Electric due to energy consumption were reduced from 500,000 tCO2 to 240,000 tCO2, which is an absolute reduction of more than 50% in just 2 years. This reduction is due to both energy efficiency efforts and the provision of renewable electricity.
Over the period 2018-2020 of the “Factory of the Future 4.0” program, energy efficiency gains have reduced CO2 emissions by approximately 47,000 tCO2 (7,000 tCO2 in scope 1, and 40,000 tCO2 in scope 2).
Amount of energy consumed by Schneider Electric globally: 1.2 TWh per year (70% electricity, 25% natural gas, 5% other).
Details of energy and CO2 reporting are available in the group’s annual report.
Key points
Invested amount
10 M € per year
Starting date of the project
January 2018
Project localisation
Worldwild
Project maturity level
Prototype laboratory test (TRL 7)
Real life testing (TRL 7-8)
Pre-commercial prototype (TRL 9)
Small-scale implementation
Medium to large scale implementation
Economic profitability of the project (ROI)
Short term (0-3 years)
Middle term (4-10 years)
Long term (> 10 years)
Illustrations of the project
This project contributes to the following SDGs:
- SDG 6 Clean water and sanitation: EcoStruxure tools help prevent lea kage and control water consumption;
- SDG 7 Clean and Affordable Energy: with the implementation of this project, there is a decrease in energy consumption;
- SDG 9 Industry, Innovation and Infrastructure: EcoStruxure improves the overall management of the site by integrating the energy
Reproducible project at all industrial sites (factories and logistics sites), with significant energy and CO2 emissions savings throughout France.
The project is piloted and deployed internally.
The World Economic Forum awarded a factory in Schneider Electric in France, located in Vaudreuil, with the label “Vitrine Industrie du Futur” (“Industry of the Future Showcase”) for the promotion of the Fourth Industrial Revolution.
Contact the company carrying the project :
jean.miyeli@se.com