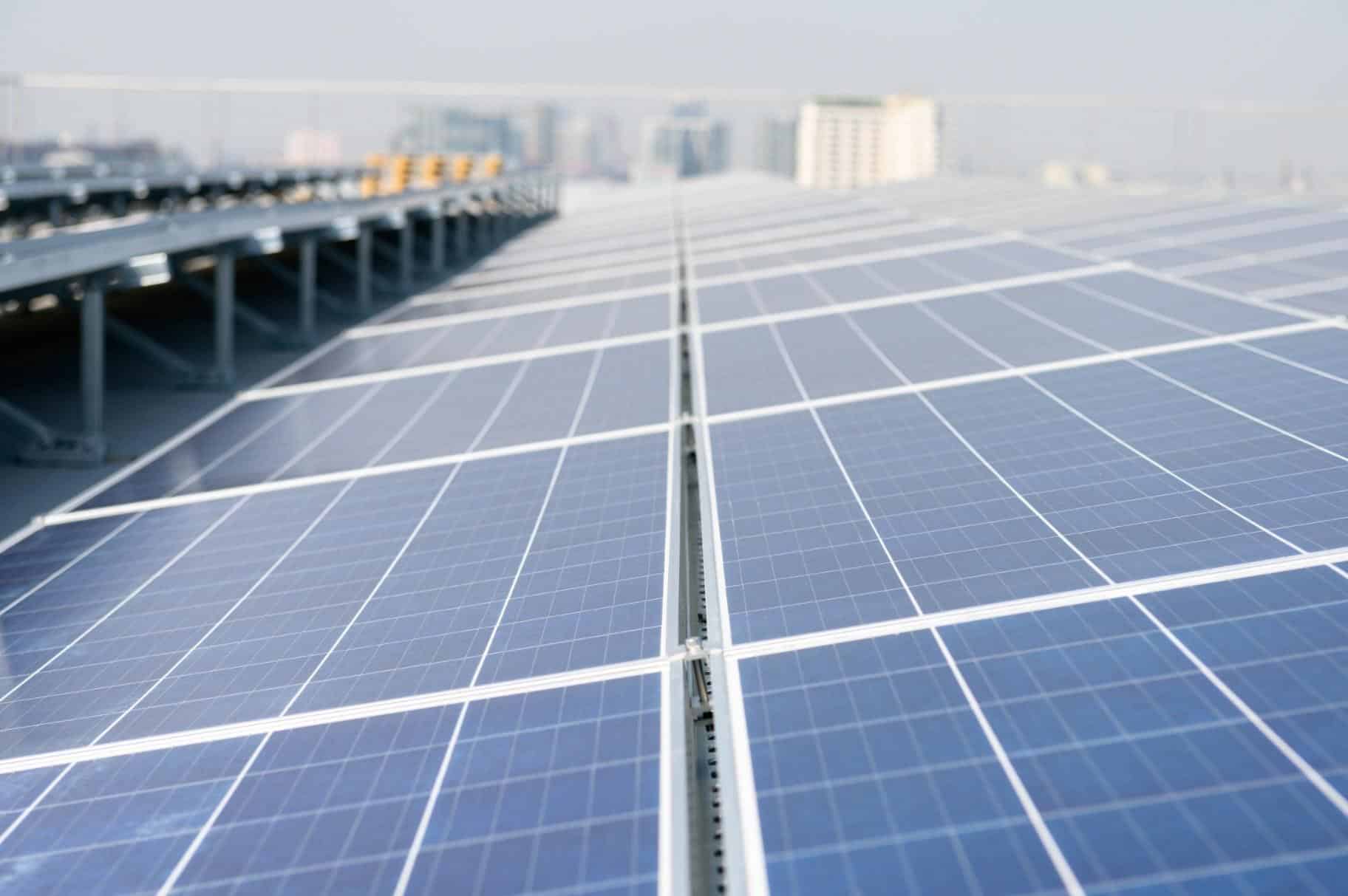
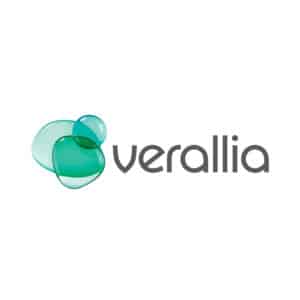
Installation of photovoltaic panels on the Mondego site, Portugal
This project aims at the production and self-consumption of solar energy on the Verallia site in Mondego, Portugal, through the installation of photovoltaic panels..
The project consists in increasing the capacity of the white cullet "de-mixing" of the Everglass Rozet Saint Albin (Haut de France), in order to increase the cullet rates in the white glass furnaces, which allows a reduction in energy consumption and CO2 emissions.
Cullet is glass that is recycled. Cullet can be made from coloured glass or white glass.
In a glass furnace, cullet replaces new mineral material (sand, soda, limestone + various other materials…).
The introduction of cullet into glass furnaces reduces the consumption of natural gas and raw materials in the furnace and therefore the raw materials in the furnace and therefore the associated CO2 emissions. Verallia’s coloured glass furnaces
Verallia’s coloured glass furnaces are saturated with cullet. To increase the cullet content in the white glass furnaces, it is necessary to increase the capacity of the furnaces, it is necessary to increase the white glass removal capacity of cullet processing sites.
New generations of optical sorting machines can achieve a white glass purity of 99,8%.
To achieve this, it is necessary to modify the existing installations to include new optical sorting machines in cascade. This also leads to the implementation of new means related to bulk handling: conveyors, lifts, vibrating distributors, silos, etc.
on which the project has a significant impact
Scope 1 – Réduction de la consommation de gaz naturel et de matière première
Avant le lancement du projet, la consommation de gaz naturel des 4 fours concernés de Chalon sur Saône et Lagnieu était de l’ordre de 619 GWh PCI/an. La réalisation de ce projet à permit permettra de réduire cette consommation de 2.4%. En utilisant un facteur d’émission de 187 kgCO2/MWh PCI, cela représente un gain de CO2 de l’ordre de 2748 tCO2/an.
Par ailleurs, la mise en œuvre de 30 000 T de calcin blanc à la place de matière “neuve” permet d’économiser 36 000 T de matière neuve. En considérant un facteur d’émissions de 180 Kg CO2/t de matière neuve fondu, cela représente un gain de CO2 de l’ordre de 5400 tCO2/an.
Forecasted investment = 3,66 M€
Q1 2022
Rozet-Saint-Albin, Aisne
This project strengthens the circular economy by developing the recycling of household glass.
This project can be replicated in all household cullet processing sites in any country.
A partnership with ADEME is awaiting validation in the framework of the call for projects for the decarbonisation of Industry.
corporate.communication@verallia.com
This project aims at the production and self-consumption of solar energy on the Verallia site in Mondego, Portugal, through the installation of photovoltaic panels..
In 2018, Verallia initiated a process to identify and activate levers for reducing the energy consumption of the industrial processes implemented at its sites (excluding melting). Identify and activate levers for reducing…