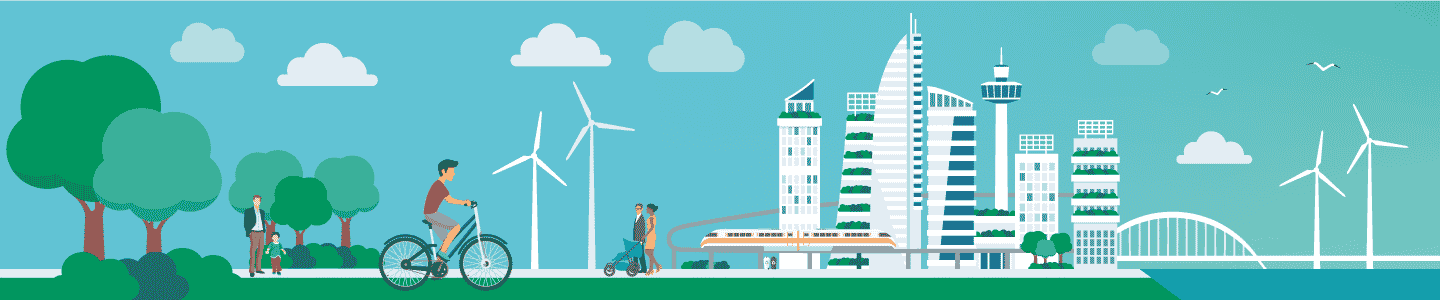
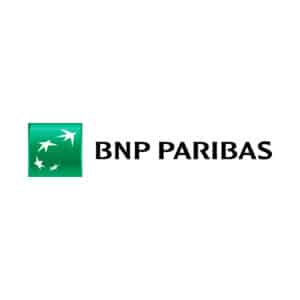
Launch of BNP Paribas Energy Transition fund
Launched in 2019, the BNP Paribas Energy Transition Fund invests in energy transition opportunities arising from increased energy demand, changing energy mix and the need…
Thanks to its wood frame structure, the Curve building meets the necessary need to reduce carbon emissions of the real estate industry.
With nearly 24,000 m2 of office space out of 7 levels, Curve is one of the largest wood structure buildings in Europe. The building runs on seven floors and four basement levels and has 1960 workstations. Located near the “Stade de de France” station on the RER B, Curve offers a wide range of services (business centre, co working, fitness, concierge, contemporary coffee, etc.), including several accessible terraces and generous landscaping gardens. The trays of nearly 3,000 m2 have a free height above 2.70m and a depth of about 18m.
The stairs and elevators cores are made of low carbon concrete (as are the infrastructure) and ensure the bracing and thermal inertia of the building. Mixed wood and concrete construction, as well as the implementation of the majority of CLT load-bearing walls (prefabricated), reduces the carbon impact relative to a traditional concrete structure and ensures carbon storage of 4,200 tons of CO2.
This constructive method, which relies heavily on pre manufacturing, also offers the advantage of the speed of onsite installation, allowing for a gain in terms of the execution schedule.
Anodished aluminium sun-shadings also protect the façade.
Other examples of carbon optimisation:
The building is committed to 40% below RT2012 in terms of its energy needs, aiming for HQE certification under the NF referential for tertiary buildings – starts HQE from 2015, with an Exceptional level passport, the Effinergie + label as well as the E + C level E2C1 and the BBCA level Standard label.
on which the project has a significant impact
Scope 1 – Achievement of the BBCA level Excellence label as well as the E + C1 level E2C1 label :
873.4kgCO2eq/m ² or 20,950 tons of CO2 (Quantifying E+C-, Eges PCE (Materials-related GHG))
Scope 2 – Optimising the energy performance of the built and systems, in order to achieve E2 level (RT-30% equivalent) :
Scope 2 – Recours au réseau de chaleur vertueux de Saint-Denis (0.116 gCO2/kWh) :
215 kgCO2eq/m ² or 5,150 tons of CO2 for 50 years (Quantifying E+C-: Energy Eges)
4.3 kgCO2eq/m ² or 103 tons of CO2 per year (Energy Eges)Emissions absorption – Setting up CLT floors/sails and LC poles :
La méthodologie E+C- a été utilisée pour les calculs et ordres de grandeurs présentés ci-dessus. Il s’agit d’une méthode de calcul des indicateurs relatifs au bilan énergétique et à la performance environnementale du bâtiment sur l’ensemble de son cycle de vie, notamment au regard des émissions de gaz à effet de serre. Il a été mis en place par les ministères de la transition énergétique et de la cohésion territoriale, et vient en complément de la réglementation thermique actuelle applicable aux bâtiments neufs (RT 2012).
Cette approche permet ainsi de définir les émissions de CO2 sur les périmètres suivants notamment :
Not disclosed
2017
Saint-Denis, Seine-Saint-Denis
Non communiqué
During the project, residents were able to enjoy a dry, silent and fast mounting. Four months were required in total to mount the seven levels pre-manufactured bone.
A 250 m2 brewery will be installed at ground floor
With its cinded facades and unfamiliar, winding appearance, Curve not only puts a spotlight on timber construction and technical know-how, but also on the Montjoie district, where the Woodwork worksite, also in wood, is being completed.
The building will now be the new headquarters of the ARS (Regional Health Agency). It will bring together teams once installed in the Millennium at Porte d’Aubervilliers and the Seine Saint Denis annexe in Bobigny. The purpose of this internal gathering is to facilitate coordination and exchange in the deployment of operations in the different territories. The significant reduction in the rent generated will be reinvested to enable the development of new actions.
The column/beam structure typology as well as the use of wood could be renewed and implemented on another construction project.
jean-marc.vincent@realestate.bnpparibas
Launched in 2019, the BNP Paribas Energy Transition Fund invests in energy transition opportunities arising from increased energy demand, changing energy mix and the need…
AFEP (Association of French large companies) is an association representing 111 of the largest companies operating in France. It participates in the public debate with the ambition to provide pragmatic answers in favour of the development of a competitive and sustainable French and European economy, conducive to the growth of all companies.