Ballast project: transporting Perrier brand products by rail
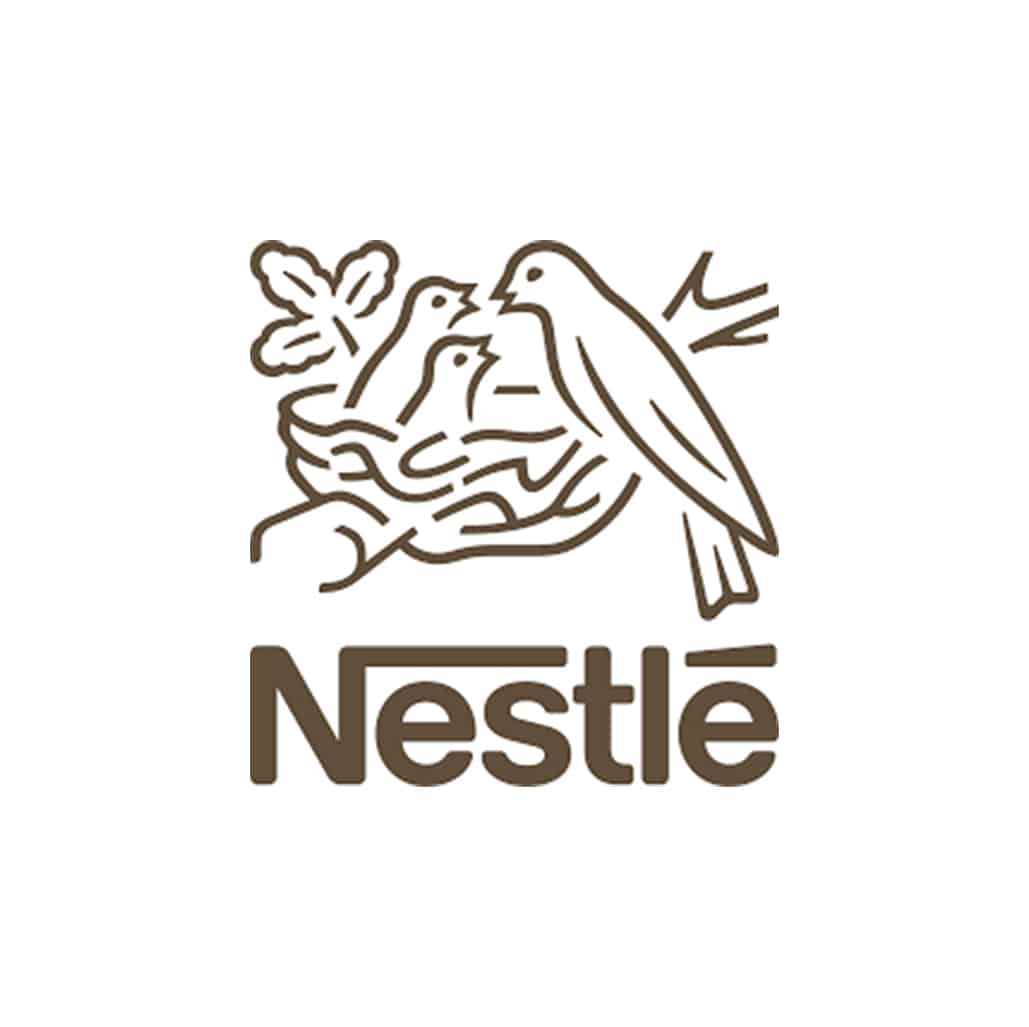
The rehabilitation of railway infrastructures and the construction of a multimodal platform at the Perrier plant in Vergèze allows the Perrier brand to achieve a modal shift from road to rail for the transport of its products to the port of Fos-sur-Mer and thus reduce the associated CO2 emissions.
Main project's drivers for reducing the greenhouse gas (GHG) emissions
Energy and resource efficiency
Energy Decarbonisation
Energy efficiency improvements
Improving efficiency in non-energy resources
Emission removal
Financing low-carbon issuers or disinvestment from carbon assets
Reduction of other greenhouse gases emission
Project objectives
The project aims to reduce the CO2 emissions linked to the transport of the Perrier brand by exporting its products by rail rather than road.
At the same time, the project relieves the road congestion between the Perrier factory in Vergèze in the Gard department and the Port of Fos-Sur-Mer in the Bouches-du-Rhône department, over a distance of approximately 100kms.
Through Ballast, Perrier is responding to more global issues. Last July, the brand committed to achieving carbon neutrality by 2022. This neutrality is one of the components of the Nestlé Group’s commitment to reach net zero emissions by 2050 in compliance with the Paris agreements. As transport accounts for around 39% of the Perrier brand’s emissions*, Ballast is therefore part of the group’s efforts to reduce emissions.
The relaunch of the rail line between the industrial site of Vergèze (Gard) and the port of Fos-sur-Mer (Bouches-du-Rhône) enables the Perrier brand to transport 70% of its maritime exports by rail, i.e. nearly 13,500 containers per year.
As a result, the Ballast project is having a positive impact on reducing the brand’s carbon footprint by switching from diesel trucks to an 80% electric train, reducing Perrier’s dependence on oil.
This process also improves the traffic flow. The Ballast project has a positive impact on urban areas by relieving congestion on the roads linking the plant to the port of Fos-sur-Mer, an area that is particularly saturated between Monday and Friday.
* The three main categories that make up Perrier’s carbon footprint are logistics (including transport) at 41%, packaging at 41% and manufacturing at 12%.
Emission scope(s)
on which the project has a significant impact
- Emission scopes
- Description and quantification of associated GHG emissions
- Clarification on the calculation
Scope 1
Direct emissions generated by the company's activity.
Scope 2
Indirect emissions associated with the company's electricity and heat consumption.
Scope 3
Emissions induced (upstream or downstream) by the company's activities, products and/or services in its value chain.
Emission Removal
Carbon sinks creation, (BECCS, CCU/S, …)
Avoided Emissions
Emissions avoided by the activities, products and/or services in charge of the project, or by the financing of emission reduction projects.
Scope 1 – Modal shift from road to rail for freight transport
- Quantification : – 2,2 ktCO2eq/year
Based on the operational data below, the Ballast project makes it possible to move from an initial situation of road transport via 44T lorries loaded to 24T, making the Vergèze-Fos-sur-Mer journey and consuming an average of 31.77 litres/100km to a rail flow over the same distance.
Data:
- 297 570.0 tonnes
- 256 294 800 litres transported
- 12469 trucks
- 90 km distance
- 50% average empty distance rates
The calculation of the emissions associated with this road transport flow consists of multiplying the litres consumed (713,068) by the emission factor for diesel fuel (3.16kgsCO2/litre) and dividing the result by 1,000 to obtain tCO2eq. This brings us to 2,253.29tCO2eq The calculation of the emissions associated with the rail flow consists of multiplying the tonnes / kms (31,270,140) by the rail emission factor in gco2 / t.km (1.67Gco2 / t.km) and dividing the result by 1 000 000 to obtain tCO2eq. This brings us to 52.22tCO2eq. In the end, 2,201 tCO2eq were avoided by switching from road to rail transport.
Key points
Invested amount
2 M €
Starting date of the project
October 2018
Project localisation
Vergèze, Gard
Project maturity level
Prototype laboratory test (TRL 7)
Real life testing (TRL 7-8)
Pre-commercial prototype (TRL 9)
Small-scale implementation
Medium to large scale implementation
Economic profitability of the project (ROI)
Short term (0-3 years)
Middle term (4-10 years)
Long term (> 10 years)
Illustrations of the project
The project responds to SDG 7 “Affordable and Clean Energy”, by reducing dependence on diesel, switching from trucks to 80% electric train journeys.
It responds to SDG 9 “Industry, Innovation and Infrastructure”, by innovating and investing in greener and more sustainable transport modes.
The project responds to SDG 11 “Sustainable Cities and Communities”, by relieving road congestion between the Vergèze plant and the Port of Fos-sur-Mer, but also by reducing transport-related noise pollution by 10-15% for the local population.
Finally, we are responding to SDG 12 “Responsible Consumption and Production” by reducing the environmental impact of our products, since the volumes now transported by train represent 43%* of the global volumes of the Perrier brand.
* According to the LCA study conducted by RDC on 2018 volumes.
Nestlé is committed to reducing its GHG emissions to achieve net zero emissions by 2050.
Following on from the ‘Ballast’ project, Nestlé Waters has undertaken other projects. For example, in 2019, Vittel (a Nestlé Waters brand), in partnership with VFLI (a subsidiary of the SNCF), replaced a train running on diesel over a distance of 600kms between the Vittel factory in the Vosges and Arles with the first European dual-mode hybrid train EURODUAL, which makes almost all of its journey in electric mode (565kms)
These various projects are in line with the government’s desire to increase the share of rail freight in France, reaffirmed last July.
Ballast was created in barely a year, a record for a project of this scale. The conditions for this success are reflected in the seamless collaboration between private and public actors.
As part of this project, numerous partnerships have been set up with:
- Perrier
- Région Occitanie
- SNCF Réseau/SNCF Infra
- RégioRail
- Amsted Digital Solutions
- Arnal
- Bolloré Logistics
- Brifer
- Combronde
- Ermewa
- Eurofos et Seayard
- Grand Port Maritime de Marseille
Finally, this project, carried out in partnership with the SNCF Réseau and other actors, has enabled investment in a more responsible and sustainable mode of transport that benefits everyone.
Contact the company carrying the project :
Communication.Nw@waters.nestle.com