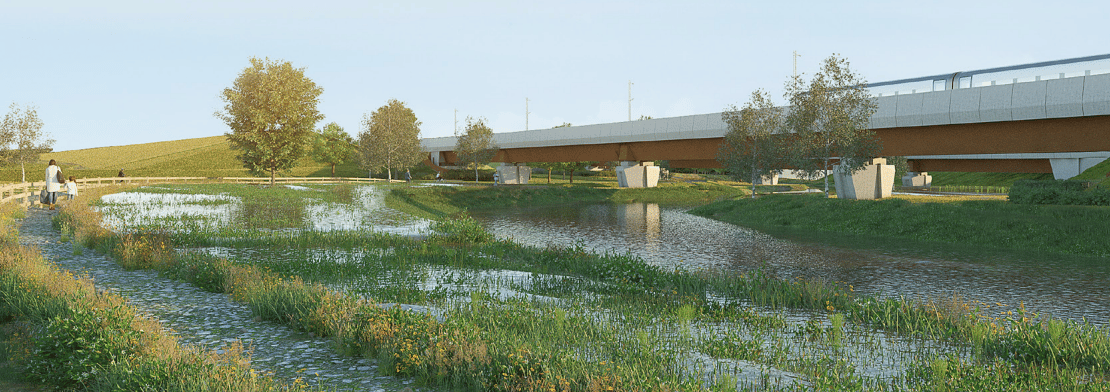
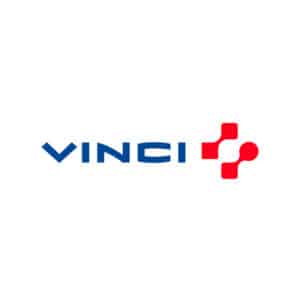
LGV High Speed II
The Balfour Beatty VINCI joint-venture is responsible for the design and construction of part of Europe’s most ambitious rail project: HS2…
Massifying thermal renovations to accelerate the ecological transition
Large prefabricated panels for external insulation in rehabilitation.
on which the project has a significant impact
Scope 1 /2/3 : Better energy efficiency. The product has been designed to be completely dismantled (in parts or as a whole) and recyclable.
Quantification : Over the entire life cycle of the product, the associated greenhouse gas emissions (production, transport, installation, end of life) are of the order of 100 tCO2/energy renovation project, i.e. about 25% less than a conventional renovation solution.
Emissions Absorption : Possibility of using bio-based insulation (wood wool).
Avoided Emissions : On average, upgrade from an E to a C energy label depending on the demands of the clients. All performances can be targeted, including passive buildings.
Quantification : Changing the energy label from E to C reduces the emissions of a house by an average of 3 tCO2/year in France.
The environmental impact was calculated using the simplified Life Cycle Assessment methodology established by VINCI and validated by a scientific committee.
According to this method, the emissions associated with the production of the product (materials, design, assembly) are evaluated at 8.7 teCO2; the emissions due to the installation of the product are evaluated at 1.46 teCO2 and at the end of life the materials can be recycled which would bring a benefit evaluated at 0.77 teCO2.
Changing the energy label from E to C allows for an average energy saving of 16,000 kWh/year on a dwelling in France for heating and cooling. With an average emission factor of 188 geCO2/kWh for heating and cooling in France, we obtain avoided emissions of 3 teCO2/year on average for a dwelling.
2M€
01/01/2019
Metropolitan France / Europe
Circular economy
The design of the product, which can be completely dismantled (by elements or in its entirety) and recycled, allows it to be integrated into value chains for the management of the end of the building’s life and for the recycling and reuse of construction waste.
The first Rehaskeen projects are currently being installed. Their design makes it possible to dismantle them and integrate them into the recycling chains, as practiced by the Group’s businesses. At this stage, no product has had to be dismantled and recycled. It is therefore premature to illustrate this example in greater detail, as the first cases of use will come in possibly 20 to 30 years.
The first prefabrication workshop was set up in the Ile de France region. Eventually, a national deployment is planned with a prefabrication workshop in each region. The model can be replicated in Europe.
rehaskeen@vinci-construction.fr
The Balfour Beatty VINCI joint-venture is responsible for the design and construction of part of Europe’s most ambitious rail project: HS2…
Deployment of an integrated charging solution for electric vehicles powered by renewable energy.
The Power Road® system deployed by Eurovia captures and recovers up to 25% of the sun’s heat energy which is then used to heat buildings and equipment located near the roadway.
VINCI Construction is stepping up the pace of sustainable construction by promoting types of concrete with lower carbon emissions. With the launch of its new Exegy
The Greenfloor solution deployed by Vinci Energies’ subsidiary I.C. Entreprise reduces the amount of energy used to regulate the temperature of buildings.