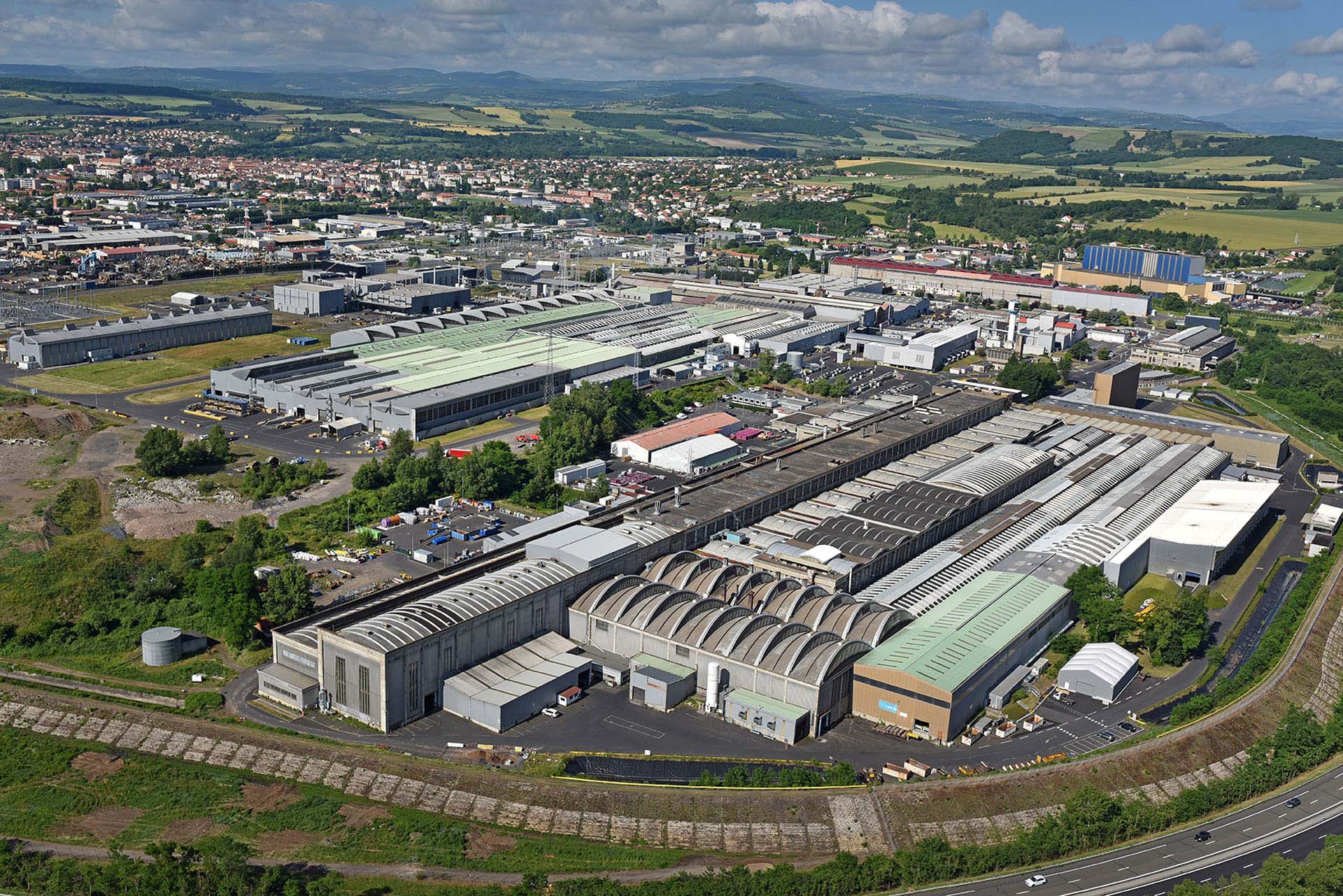
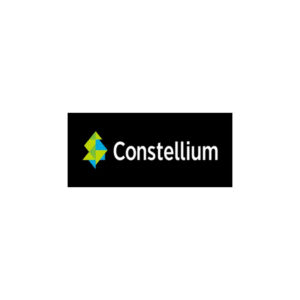
Energ’Iss, heating the city of Issoire with our casting furnaces
This project, conducted with Dalkia and the city of Issoire, will make it possible to use the waste heat from the foundry furnaces of our industrial site located …
Type of climate innovation of the project with a description of the problem/issue addressed.
The objective is to reduce by almost 90% the greenhouse gas emissions contained in the metal used by recycling our customers' production scrap and end-of-life products and thus avoiding the purchase of primary aluminum, which is electricity-intensive and a source of emissions. (source: European Aluminium Association)
It is also to promote the circular economy, the can at the end of its life being recycled to make a new can and the scrap of automobile production to make new hoods for example.
The Neuf-Brisach site includes a recycling process, a foundry and the production of semi-finished products resulting from the lamination of aluminium plates into coils or sheets.
The project consists of investing in 2 recycling furnaces capable of processing 130,000 tons of scrap and feeding the foundry furnaces and then the rolling lines, to produce coils or sheets for the production of cans or car bodies.
The Neuf-Brisach site already has a recycling capacity of 150,000 tons.
On average, for 1 ton of scrap, we obtain 930 kg of recycled aluminum.
NB: this amount may vary depending on the type of scrap (quality, size, alloy).
on which the project has a significant impact
Scope 3 –Avoid using primary aluminum.
Quantification: Reduction of 450 000 T of eq CO2
The average primary aluminum in Europe has a footprint of 6.8 tons of CO2 per ton of primary aluminum produced and low carbon suppliers reach levels of 4 tons. These emissions are mainly related to energy use during production (bauxite mining, refining, electrolysis).
The planned facilities will produce an additional 130,000 tons of recycled aluminum. To be conservative, we have considered that they would replace the lowest carbon equivalent of primary aluminum, i.e. with a footprint of 4 tons of CO2/tonne. Considering that the carbon footprint of recycling (0.5 TCO2/tonne of recycled aluminium), we obtain a reduction of the order of :
130,000 tons x (4 – 0.5) = 450,000 TCO2/year
150 million euros
2021
Neuf-Brisach, in Alsace
By avoiding the production of primary aluminum, we avoid the use of bauxite mining (impact on biodiversity but also on indigenous populations, given its location), the production of alumina and the storage of bauxite residues. We promote the circular economy.
We can launch this project in other aluminium transformation plants with of course adaptations in terms of size and technology of furnace according to the treated scrap and produced alloys.
The project has received support from the France 2030 stimulus plan. We have carried out a public consultation, notably for the environmental assessment of the project, and we are working with a network of equipment suppliers and subcontractors.
antti.laakkonen@constellium.com
This project, conducted with Dalkia and the city of Issoire, will make it possible to use the waste heat from the foundry furnaces of our industrial site located …